Understanding the Laser Welder Cost: A Comprehensive Guide
When you’re looking into investing in welding technology, especially in industries like manufacturing, construction, and jewelry, one of the most crucial aspects to consider is the laser welder cost.
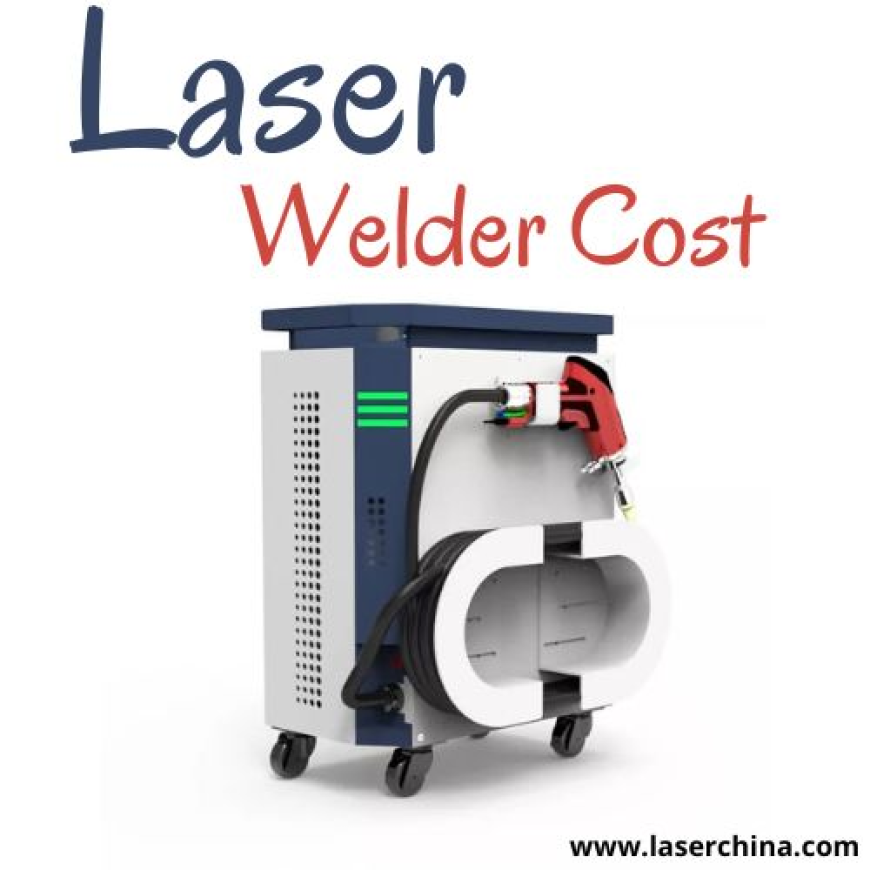
The decision to invest in laser welding machines involves more than just an initial purchase price; it’s important to evaluate the total cost of ownership over time, including maintenance, consumables, and the machine’s longevity. This guide will break down all the factors that influence the laser welder cost, helping you make an informed decision.
Factors Affecting Laser Welder Cost
1. Machine Type and Power
The type of laser welding machine you choose will have a significant impact on the cost. For example, fiber laser welders are generally more expensive than CO2 laser machines due to their advanced technology and the precision they offer. The power of the laser also affects the price—higher-powered machines capable of handling more demanding welding tasks will typically be more expensive than lower-powered models used for light-duty work.
2. Brand and Manufacturer
As with most equipment, the brand and manufacturer play a major role in determining the cost. Well-established manufacturers often price their machines higher, but they offer greater reliability, support, and advanced technology. If you're considering a lesser-known brand, the initial cost might be lower, but you could risk facing challenges in terms of quality or customer service.
3. Laser Type
The laser welder cost is also influenced by the type of laser being used. Common options include fiber lasers, diode lasers, and CO2 lasers. Fiber lasers, while highly efficient and precise, tend to have a higher initial price tag. On the other hand, CO2 lasers may be more affordable but may not offer the same level of efficiency and versatility for all types of welding applications.
4. Automation and Features
Machines with more automation features, such as robotic arms or automated feeding systems, come at a higher cost. These automated systems can significantly increase production efficiency, but they add complexity and cost to the overall price. Some machines offer advanced features such as programmable controls, multiple welding modes, and easy integration with CAD systems, all of which contribute to higher prices.
5. Size and Weight
The physical size and weight of a laser welder can also impact its cost. Larger, more robust machines capable of handling heavy-duty industrial tasks tend to be pricier than compact machines suited for smaller operations or niche applications. If you need a machine that can handle large materials or work in a larger scale environment, you’ll be looking at a higher investment.
Total Cost of Ownership
When evaluating the laser welder cost, it's crucial to consider the total cost of ownership, which includes not only the upfront price but also the ongoing operational and maintenance costs. Here are some key components that contribute to the total cost:
1. Maintenance Costs
Laser welding machines, like all complex equipment, require maintenance to ensure longevity and optimal performance. Over time, the laser optics and components may need to be cleaned or replaced. The maintenance costs will vary depending on the machine’s brand, complexity, and usage. Machines with advanced features or automation systems may have higher maintenance costs, while simpler models could be more cost-effective to maintain.
2. Energy Consumption
Laser welding machines can be energy-intensive, especially those with high-power lasers. The amount of energy the machine consumes will directly affect your operating costs. It’s important to consider the energy efficiency of the machine you plan to purchase, as more energy-efficient models can help reduce long-term operating costs.
3. Consumables and Spare Parts
Consumables such as laser lenses, nozzles, and gases (like nitrogen or oxygen) are essential for maintaining optimal welding performance. Over time, these parts wear out and need replacement. The cost of consumables can vary depending on the type of laser welder and the materials being welded. Be sure to factor these recurring costs into your decision-making process.
4. Training and Operator Costs
When you purchase a laser welding machine, you'll likely need to train your operators to use the equipment effectively. Some machines come with advanced control systems that require specialized training, which can add to the cost. Additionally, operators who are proficient in using laser welders may command higher salaries compared to those trained in traditional welding methods.
Comparing Laser Welder Cost to Traditional Welding Methods
Traditional welding methods such as MIG (Metal Inert Gas), TIG (Tungsten Inert Gas), and Stick welding are typically much less expensive in terms of initial investment compared to laser welders. However, they come with their own set of limitations, such as lower precision, slower speeds, and higher consumable usage rates.
When comparing laser welder cost to traditional methods, it's essential to evaluate the following:
-
Precision and Speed: Laser welding offers significantly higher precision and speed than traditional welding, which can translate into higher productivity and reduced waste in the long term. This means that even though the initial cost is higher, a laser welder could pay for itself by increasing the efficiency of your operations.
-
Material Compatibility: Laser welding can be used on a wider range of materials, including metals like stainless steel, aluminum, and even exotic materials like titanium, which might be difficult to weld using traditional methods. The ability to work with a broader range of materials makes laser welders highly versatile.
-
Labor Costs: Laser welders often require fewer operators due to automation, which can reduce labor costs. On the other hand, traditional welding methods are more labor-intensive, requiring skilled welders to handle the equipment.
-
Quality of Welds: Laser welds are often stronger and cleaner than traditional welds, resulting in better-quality finished products. For industries that require high-quality and aesthetically pleasing welds, the laser welder cost may be justified by the superior results it offers.
Financing Options for Laser Welders
Given the high initial cost of laser welders, many businesses explore financing options to ease the financial burden. There are several ways to finance the purchase of a laser welder:
-
Leasing: Leasing allows you to spread the cost of the equipment over time, making it more affordable. It’s an attractive option for businesses that need to conserve capital but still want access to advanced technology.
-
Loans: Securing a loan is another way to finance your laser welder purchase. With this option, you own the machine outright after paying off the loan. The terms and interest rates will depend on your credit history and the lender’s policies.
-
Government Grants and Subsidies: In some cases, government programs may offer financial assistance or tax incentives for businesses that invest in advanced manufacturing technologies like laser welding. Be sure to research if there are any grants or subsidies available in your area.
Final Thoughts
In conclusion, the laser welder cost is influenced by a range of factors, including the type of machine, brand, and additional features such as automation and advanced controls. While the initial investment for laser welding machines can be high, the increased efficiency, precision, and ability to weld a broader range of materials often make it a worthwhile investment for businesses that require high-quality welding. When evaluating the cost, it’s important to consider not just the upfront price but also the ongoing operational costs, including maintenance, consumables, and energy consumption. By carefully considering all of these factors, you can make an informed decision that will serve your business needs for years to come.