The Role of HSE in Preventing Industrial Accidents in Malaysian Engineering Firms
Explore how strong HSE practices help Malaysian engineering firms prevent industrial accidents and build a safer, more resilient workplace environment.
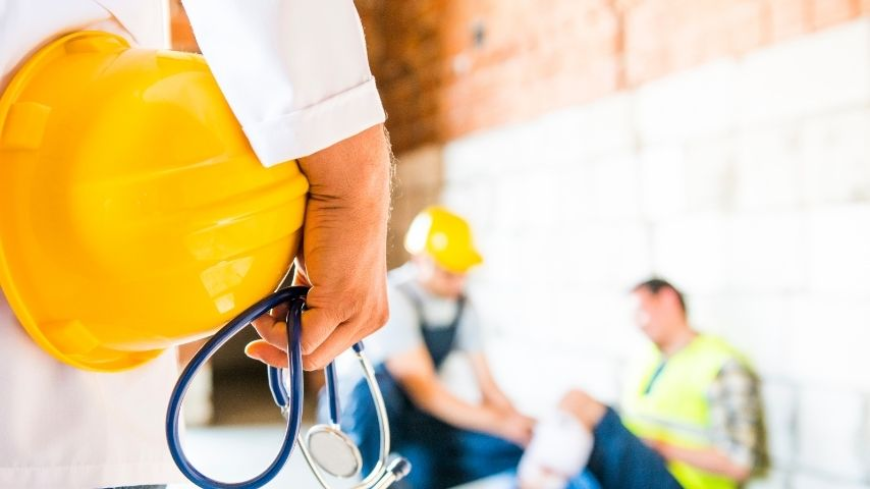
Industrial accidents in Malaysian engineering firms can have devastating consequences, affecting both human lives and business operations. Health, Safety and Environment (HSE) practices play a crucial role in preventing these workplace incidents.Yet, many organizations still struggle with effective safety management.
Whether you're an HSE professional, engineering manager, or business owner in Malaysia's industrial sector, understanding these critical safety practices is vital for protecting your workforce and maintaining operational excellence. Let's dive into the fundamental aspects of HSE implementation that can transform your workplace safety culture.
Evolution of HSE in Malaysian Engineering Industry
The Malaysian engineering industry has witnessed a remarkable transformation in its approach to workplace safety and health over the decades. This evolution reflects the nation's growing commitment to protecting its workforce while adapting to international standards and technological advancements.
Key Historical Milestones
The history of workplace safety in Malaysia began during the British colonial period, primarily focusing on basic industrial regulations. The first significant step was the introduction of the Machinery Ordinance in 1953, which laid the foundation for modern safety practices in engineering firms.
The historical trajectory of workplace safety gained momentum in the 1960s when Malaysia established its first dedicated safety organization, the Factory and Machinery Department. This marked a crucial turning point in institutionalizing safety protocols across the engineering sector.
The 1970s saw the implementation of the Factories and Machinery Act 1967, which brought comprehensive guidelines for machinery operation and maintenance. This legislation became a cornerstone for engineering safety practices, introducing regular inspections and certification requirements.
A major leap forward occurred in 1994 with the enactment of the Occupational Safety and Health Act (OSHA). This landmark legislation expanded the scope of workplace safety beyond just physical hazards, incorporating health and environmental considerations. It mandated the formation of safety committees in engineering firms and introduced systematic risk assessment procedures.
The early 2000s witnessed the integration of international safety standards, with Malaysian engineering firms adopting ISO certifications and global best practices. This period also saw the emergence of specialized safety training programs and the development of industry-specific safety guidelines.
Recent years have brought digital transformation to HSE practices, with engineering firms implementing smart monitoring systems, automated safety protocols, and data-driven risk management approaches. This technological integration has significantly enhanced the effectiveness of safety measures while reducing incident rates.
Regulatory Framework and Compliance Requirements
Government Bodies and Their Roles
In Malaysia, workplace safety and health regulations are overseen by multiple government bodies, each playing a crucial role in ensuring compliance and protection of workers. The Department of Occupational Safety and Health (DOSH) serves as the primary regulatory authority, operating under the Ministry of Human Resources.
DOSH enforces the machinery act, which establishes fundamental safety requirements for industrial equipment and operations. Factory inspectors, appointed under this act, conduct regular site visits to ensure compliance with safety standards and investigate workplace incidents.
The National Institute of Occupational Safety and Health (NIOSH) complements DOSH's regulatory function by providing training, research, and consultancy services. They work closely with industry stakeholders to develop and implement effective safety protocols.
The main provisions of the ordinance are enforced through a systematic approach, involving regular audits, inspections, and compliance monitoring. These provisions cover various aspects of workplace safety, from equipment maintenance to emergency response procedures.
The Social Security Organisation (SOCSO) plays a vital role in providing social protection for workers affected by occupational accidents and diseases. They work in tandem with other regulatory bodies to ensure comprehensive worker protection.
The Ministry of International Trade and Industry (MITI) contributes to the regulatory framework by establishing safety standards for industrial processes and international trade compliance. They collaborate with factory inspectors to maintain quality control and safety measures in manufacturing facilities.
Local authorities also participate in enforcement through building codes and environmental regulations that impact workplace safety. Their involvement ensures that safety measures are implemented at both national and local levels.
These regulatory bodies maintain a collaborative approach, sharing information and resources to create a comprehensive safety network. Their combined efforts help establish and maintain high safety standards across Malaysian engineering firms.
Core Components of HSE Management
A robust HSE management system forms the backbone of workplace safety in Malaysian engineering firms. It encompasses various interconnected elements that work together to create a secure work environment while ensuring regulatory compliance and operational efficiency.
Risk Assessment and Control Measures
Risk assessment serves as the foundation of effective HSE management, particularly in environments where occupational safety is paramount. This systematic process involves identifying potential hazards, evaluating their severity, and implementing appropriate control measures to minimize risks.
In Malaysian engineering firms, comprehensive safety management systems typically follow a hierarchical approach to risk control:
- Elimination: Removing the hazard completely
- Substitution: Replacing hazardous materials or processes with safer alternatives
- Engineering Controls: Installing physical barriers or modifications
- Administrative Controls: Implementing safe work procedures and training
- Personal Protective Equipment: Providing appropriate safety gear as a last line of defense
When dealing with specialized equipment like safety aspects of steam boilers, risk assessments become even more critical. These assessments must consider:
- Pressure vessel integrity
- Temperature control systems
- Emergency shutdown procedures
- Maintenance schedules
- Operator competency requirements
Regular monitoring and review of control measures ensure their continued effectiveness and allow for necessary adjustments based on changing conditions or new risks identified through incident reports or safety audits.
Building a Strong Safety Culture
Employee Engagement and Training
Creating a robust safety culture begins with active employee engagement and comprehensive training programs. When workers feel personally invested in maintaining a safer working environment, they become proactive participants rather than passive observers in safety initiatives.
Effective engagement starts with regular safety meetings where employees can voice their concerns and share insights from their daily experiences. These discussions help identify potential hazards that management might overlook and foster a collaborative approach to workplace safety.
Training plays a pivotal role in establishing a higher level of safety culture environment. It should go beyond basic compliance requirements to include:
- Regular safety workshops and refresher courses
- Hands-on practical demonstrations
- Emergency response drills
- Risk assessment training
- Peer-to-peer learning sessions
Organizations must ensure that training materials are updated regularly to reflect new safety protocols and industry best practices. This continuous learning approach helps employees stay current with safety requirements while reinforcing the importance of workplace safety.
To strengthen the safety culture, companies should implement recognition programs that celebrate employees who consistently demonstrate safety leadership. This positive reinforcement encourages others to follow suit and shows that the organization values safety-conscious behavior.
Documentation of training sessions and engagement activities serves multiple purposes:
- Tracks progress and participation
- Identifies areas needing improvement
- Demonstrates compliance with regulatory requirements
- Provides evidence of ongoing commitment to safety
By combining robust training initiatives with meaningful employee engagement, organizations can create an environment where safety becomes second nature to everyone involved.
Also read: Powerful Guide to Protective Eyewear, Safety Eyeglasses & Work Glasses: Your Vision's Best Defense
Performance Monitoring and Measurement
Safety performance monitoring plays a vital role in preventing industrial accidents within Malaysian engineering firms. It provides organizations with valuable insights into their safety practices and helps identify areas that need improvement.
Key Performance Indicators
Safety performance indicators serve as crucial metrics that help organizations track and evaluate their safety initiatives. These indicators are typically categorized into two main types: leading and lagging indicators.
Leading indicators are proactive measurements that focus on preventive activities and safety processes. They include metrics like safety training completion rates, hazard identification reports, and safety inspection frequencies.
Lagging indicators, on the other hand, measure the outcomes of past safety performance. These include incident rates, lost time injury frequency rates, and severity rates. While lagging indicators are important, they shouldn't be the sole focus of safety performance measurement as they only reflect past events.
Malaysian engineering firms often combine both types of indicators to create a comprehensive safety performance monitoring system. This balanced approach helps organizations:
- Track current safety initiatives
- Identify potential risks before incidents occur
- Measure the effectiveness of safety programs
- Compare performance against industry benchmarks
- Make data-driven decisions for safety improvements
Regular monitoring and analysis of these indicators enable organizations to maintain high safety standards and continuously enhance their safety protocols.
Addressing Psychosocial Hazards
Impact on Worker Well-being
Psychosocial hazards in Malaysian engineering firms pose significant challenges to workplace safety and employee health. These invisible threats manifest through excessive workload, poor work-life balance, and inadequate support systems, directly impacting worker performance and mental health.
Engineering professionals often face intense pressure to meet project deadlines while maintaining precision in their work. This constant stress can lead to burnout, anxiety, and decreased job satisfaction. When left unaddressed, these psychosocial hazards can create a ripple effect, compromising both individual well-being and overall workplace safety.
Organizations must implement comprehensive support programs that include regular mental health check-ins, stress management workshops, and clear communication channels. Creating a balanced work environment where employees feel valued and supported is crucial for maintaining both psychological and physical safety at work.
Strategic Planning for Accident Prevention
Implementation Framework
The development of a robust strategic plan for accident prevention in Malaysian engineering firms requires a systematic and comprehensive approach. The health master plan serves as the foundation, incorporating both immediate safety measures and long-term preventive strategies.
The OSH master plan, developed by the Department of Occupational Safety and Health (DOSH), outlines specific objectives and targets for reducing workplace accidents. This strategic program emphasizes the importance of proactive risk assessment, employee training, and regular safety audits.
To effectively implement the strategic plan, organizations should:
- Conduct thorough risk assessments across all operational areas
- Establish clear safety protocols and emergency response procedures
- Provide regular training and certification programs for employees
- Implement monitoring systems to track safety performance
- Develop incident reporting and investigation mechanisms
- Create feedback loops for continuous improvement
The success of accident prevention initiatives relies heavily on management commitment and employee engagement. Regular reviews and updates of the strategic program ensure its relevance and effectiveness in addressing emerging safety challenges.
Integration of modern technology and data analytics helps in identifying potential hazards before they lead to accidents. This proactive approach, combined with traditional safety measures, creates a comprehensive framework for accident prevention.
Also read this comprehensive article on understanding HSE principles.
Conclusion
The evolution of HSE practices in Malaysian engineering firms represents a critical milestone in the nation's industrial safety journey. Through proper implementation of comprehensive safety protocols, regular training programs, and stringent compliance measures, organizations can significantly reduce workplace accidents and create a more secure working environment. By focusing on both physical and psychosocial hazards, organizations can develop a holistic safety culture that protects their most valuable asset - their workforce. We encourage all Malaysian engineering firms to prioritize HSE implementation, stay updated with regulatory developments, and continuously enhance their safety management systems. Remember, investing in workplace safety isn't just about compliance - it's about fostering a sustainable, productive, and accident-free industrial environment that benefits everyone involved in the organization.