Wet vs. Dry Vacuum Pumps: Pros and Cons Explained for Every Industry
When selecting between wet and dry vacuum pumps, the first factor to evaluate is the nature of the gases or vapors involved in your process.
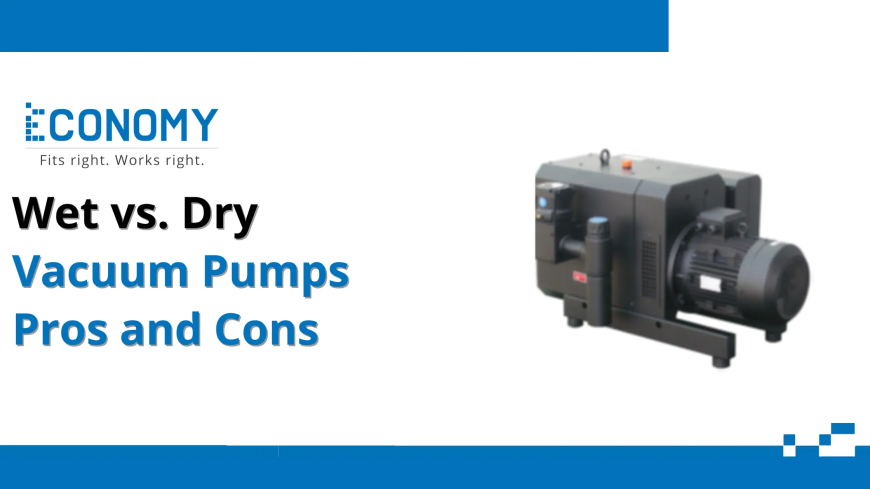
Vacuum pumps play a critical role in a wide variety of industrial applications—from pharmaceuticals and food processing to electronics, packaging, and environmental engineering. Their function is to remove air and gases from a sealed space, creating a vacuum that supports processes such as drying, degassing, and filtration. However, not all vacuum pumps work the same way. The two primary categories—wet and dry vacuum pumps—operate on different principles and are suited to different applications. Knowing the strengths and weaknesses of each type helps industries make more informed decisions for efficiency, reliability, and cost-effectiveness.
Understanding Vacuum Pumps
At their core, vacuum pumps work by reducing the pressure inside a closed system, allowing operations that require low-pressure environments to take place efficiently. They are essential in applications where air or gas needs to be extracted to facilitate chemical reactions, preserve product quality, or ensure a sterile environment. Based on the presence or absence of operating fluids in their compression chambers, vacuum pumps are categorized as either wet or dry. The choice between these two depends on a range of factors including process requirements, contamination risk, maintenance needs, and cost constraints.
What Are Wet Vacuum Pumps?
Wet vacuum pumps operate using a working fluid—typically oil, water, or a combination—which plays a key role in sealing, cooling, and lubricating the internal components of the pump. The presence of fluid allows for smoother mechanical action and more efficient compression of gases. These pumps are often used in processes where the pumped gases may contain moisture, particulates, or condensable vapors. Their fluid-based mechanism helps manage contaminants and allows them to work reliably in challenging operating environments.
Key Features of Wet Vacuum Pumps
A defining feature of wet vacuum pumps is their fluid-based internal operation, which provides a natural cushion between moving parts and helps dissipate heat generated during compression. This not only improves durability but also allows the pump to handle corrosive or aggressive gases more effectively. Additionally, the liquid used in the pump helps trap particulates and prevents damage to mechanical parts. However, wet pumps require a system to separate, clean, or dispose of the working fluid after use, which adds to maintenance and operational complexity.
What Are Dry Vacuum Pumps?
Dry vacuum pumps, as the name suggests, do not use any liquid within the compression chamber. Instead, they rely on precision-engineered rotors and chambers that compress and evacuate gases without requiring oil or water for sealing or cooling. These pumps are ideal for clean processes where contamination must be minimized. Their oil-free design makes them particularly popular in the semiconductor, pharmaceutical, and medical industries where even tiny traces of oil could compromise product integrity.
Key Features of Dry Vacuum Pumps
Dry vacuum pumps are designed for contact-free operation, meaning that internal components do not touch each other during movement. This results in lower wear and longer service life. They are generally quieter and more energy-efficient compared to their wet counterparts. Since there's no fluid to maintain or replace, they offer easier cleaning and reduced risk of backflow contamination. Their modular design also allows for quick servicing and replacement of components, making them ideal for long-term operational reliability.
Advantages of Wet Vacuum Pumps
One of the main advantages of wet vacuum pumps is their robustness in handling wet, dirty, or corrosive gas streams. The fluid within the pump helps dilute and carry away particulates and condensable vapors, making them more resilient under harsh conditions. Their design also enables them to achieve deeper vacuum levels in some applications, especially where temperature-sensitive materials are involved. They are generally more affordable upfront, making them a good choice for facilities where budget constraints are a factor and the process environment is more forgiving.
Disadvantages of Wet Vacuum Pumps
On the downside, wet vacuum pumps require regular fluid changes, cleaning, and monitoring of operating conditions to ensure performance. The need to manage spent oil or water adds environmental and logistical challenges. If the working fluid becomes contaminated, it can affect the entire pump system and potentially the product being processed. Over time, this results in higher maintenance costs and potential operational interruptions. In industries where cleanliness is a top priority, the risk of contamination from oil vapors can be a serious drawback.
Advantages of Dry Vacuum Pumps
Dry vacuum pumps excel in environments where cleanliness, low maintenance, and long operational cycles are required. Their oil-free operation eliminates the need for waste fluid management, making them more environmentally sustainable and easier to operate. Because they don’t rely on fluids for cooling or sealing, they can operate at higher temperatures without performance degradation. Their lower total cost of ownership, despite a higher initial investment, often makes them the smarter choice for high-purity processes or industries with strict compliance standards.
Disadvantages of Dry Vacuum Pumps
The biggest challenge with dry vacuum pumps is their sensitivity to process conditions. If the gas stream contains high moisture, particulates, or reactive chemicals, additional filtration or pre-treatment systems may be needed to protect the pump. This can increase both the complexity and cost of the overall setup. Additionally, their upfront cost is usually higher than wet pumps, which can be a barrier for smaller operations or pilot-scale setups.
Side-by-Side Comparison of Wet and Dry Vacuum Pumps
In practical terms, wet pumps are often the go-to option for general industrial use where gas cleanliness is not a concern and the environment is more demanding. Dry pumps, in contrast, are better suited for cleanroom environments, precision manufacturing, and processes that cannot tolerate oil contamination. Each has a well-defined space in modern industry, and their benefits are maximized when selected according to application-specific needs.
Factors to Consider When Choosing a Vacuum Pump
When selecting between wet and dry vacuum pumps, the first factor to evaluate is the nature of the gases or vapors involved in your process. Consider whether your system can tolerate oil or water contamination. Think about maintenance frequency—are you prepared for regular servicing, or do you prefer minimal intervention? Budget, compliance requirements, energy consumption, and environmental impact are also important considerations. The right vacuum pump is one that balances performance, reliability, and cost within your specific operating conditions.