How Thermographic Inspection Work?
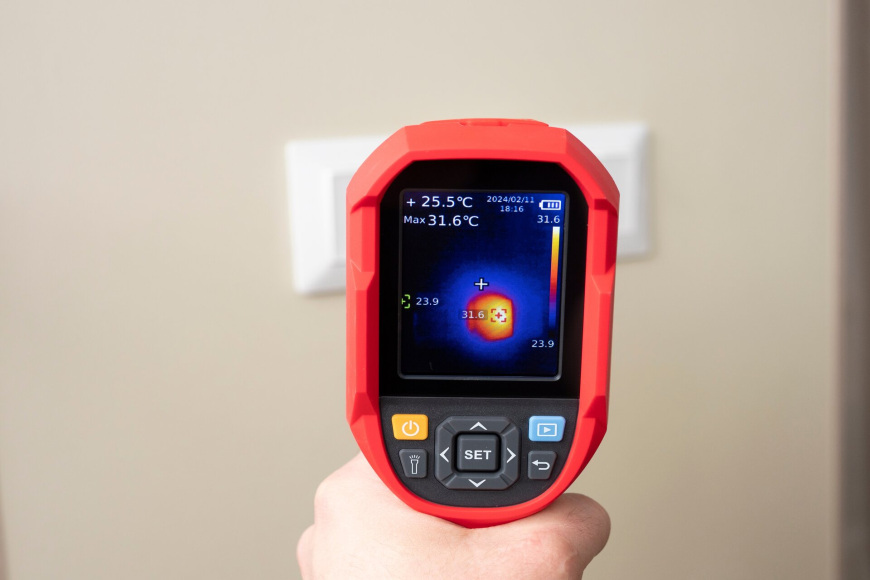
Have you ever wondered how experts manage to spot issues hidden behind walls, ceilings, or electrical systems—without tearing anything apart? The answer is through thermographic inspection. This powerful, non-invasive technique uses infrared technology to reveal problems you can’t see with the naked eye.
In this comprehensive guide, we’ll explain how thermographic inspection work, the tools professionals use, when to get one, and why it’s a smart move for homeowners, buyers, and property managers alike.
What Is a Thermographic Inspection?
A thermographic inspection—also known as an infrared inspection—uses a thermal imaging camera to measure and visualize surface temperatures. These cameras produce images called thermograms, which display different temperatures as a range of colors.
What makes thermographic inspection work so valuable is its ability to reveal underlying issues. For instance, an unusually cold section of a wall might suggest missing insulation or a draft. A warm area around an electrical panel could indicate an overheating wire.
These inspections are widely used in:
-
Residential and commercial energy audits
-
Home inspections before purchase
-
Water damage assessments
-
HVAC and insulation checks
-
Electrical safety diagnostics
Because it's non-invasive, a thermographic inspection can help you spot issues early—without damaging your home or building.
How Thermographic Inspection Work: The Tools and Technology
At the core of every thermographic inspection is a thermal imaging camera, which captures heat instead of visible light. Every object emits infrared radiation, and this camera detects those variations, turning them into an easy-to-understand image.
Understanding Thermogram Colors
In thermal images:
-
Hot areas often appear in red, orange, or yellow
-
Cooler areas show up as blue, purple, or green
These color contrasts allow inspectors to quickly identify irregularities, such as:
-
Cold patches in a wall suggesting missing insulation
-
Hot spots near electrical fixtures hinting at overloaded circuits
-
Cool areas near plumbing possibly indicating hidden moisture
Paired with regular photographs and expert analysis, thermographic cameras give a powerful visual representation of what’s happening inside your property—without opening up walls or ceilings.
When Should You Consider a Thermographic Inspection?
A thermographic inspection can be beneficial in a variety of situations. Here’s when it’s most helpful:
1. Energy Efficiency Assessments
If your energy bills are higher than expected, a thermal scan can identify areas where heat is escaping, such as leaky windows, poor insulation, or gaps in ductwork.
2. Before Buying a Property
Getting a thermographic inspection during the home-buying process can uncover hidden issues like water damage, inadequate insulation, or electrical hazards—giving you crucial insight before finalizing a deal.
3. Water Damage and Leak Detection
After flooding or plumbing leaks, thermal cameras can identify trapped moisture behind surfaces, helping prevent long-term mold and structural damage.
4. Electrical System Safety
Thermal scans can reveal overheating circuits, loose wiring, or malfunctioning components—issues that could lead to fires if not caught early.
5. Preventive Maintenance
For commercial or industrial facilities, regular thermographic inspections help monitor mechanical systems and electrical equipment for potential failures.
How Thermographic Inspection Work: A Step-by-Step Overview
Understanding how thermographic inspection work on-site gives you a better idea of what to expect. Here’s a typical process:
Step 1: Preparing the Property
To ensure accurate readings, inspectors often schedule thermal imaging during times when there’s a strong temperature contrast between the inside and outside—usually a difference of at least 20°F.
If air leaks are being assessed, a blower door test might be conducted to lower indoor pressure and draw in outside air, making leaks easier to spot.
Step 2: Thermal Scanning with Infrared Camera
The inspector uses the IR camera to scan key areas like:
-
Walls and ceilings
-
Floors
-
Windows and doors
-
Electrical panels and outlets
-
Plumbing and HVAC systems
They move methodically through the space, capturing thermal images and noting any irregularities.
Step 3: Image Interpretation
This is where professional expertise matters. Not all temperature differences are problems. Inspectors analyze the thermograms to identify patterns and determine the cause. For example:
-
Cold zones near windows might show drafts.
-
Hot spots in an attic could point to poor ventilation.
-
Warm areas near switches could indicate wiring issues.
Context matters, which is why trained professionals often take visible-light photos to match with the thermal images.
Step 4: Inspection Report and Recommendations
Once the scan is complete, you’ll receive a detailed report that includes:
-
Infrared images with annotations
-
Notes on areas of concern
-
Recommendations for repairs or further investigation
The goal is to give you a clear understanding of what’s happening in your home or building—along with practical next steps.
Benefits of a Thermographic Inspection
Now that you know how thermographic inspection work, here are the key advantages:
✔ Non-Destructive and Safe
No need to cut open walls or ceilings. Inspections are done from the surface, preserving the integrity of your home.
✔ Early Detection
Catch problems before they become major expenses—whether it's moisture damage, faulty wiring, or insulation gaps.
✔ Increased Energy Efficiency
Identifying and sealing leaks or adding insulation can significantly reduce your utility bills.
✔ Mold and Moisture Prevention
Moisture trapped behind walls can lead to mold. Thermal imaging detects it early, often before any visible signs appear.
✔ Electrical Safety
Spotting hot spots in wiring systems helps reduce the risk of electrical fires.
Limitations of Thermographic Inspections
While powerful, thermal imaging isn’t without its limits:
-
It doesn’t see through walls—it only detects surface temperature changes.
-
It can’t confirm the root cause without additional investigation.
-
Accuracy depends on proper temperature conditions during the scan.
-
It requires a trained inspector to interpret results correctly.
This is why it’s essential to hire certified professionals who know how thermographic inspection work and how to apply it effectively.
Why Choose Protec for Your Infrared Inspection?
At Protec Inspections, we specialize in delivering reliable, accurate thermographic inspections using top-tier infrared cameras and certified technicians. We don’t just take pictures—we help you understand what’s behind them.
We offer:
-
Detailed reports with thermal and visible-light images
-
Expert interpretations and honest advice
-
Customized recommendations based on your property
-
Friendly service and transparent pricing
Whether you're a homebuyer, property owner, or facility manager, we help you uncover hidden issues and protect your investment.
Final Thoughts
Understanding how thermographic inspection work can give you a major advantage in homeownership, property maintenance, or investment decisions. These inspections allow you to detect hidden issues—like heat loss, moisture, or electrical risks—without invasive testing.
If you're concerned about energy efficiency, hidden damage, or system performance, booking a thermographic inspection is one of the smartest moves you can make.
Schedule your infrared inspection with Protec Inspections today—and get peace of mind you can see.